Breaking News
Popular News
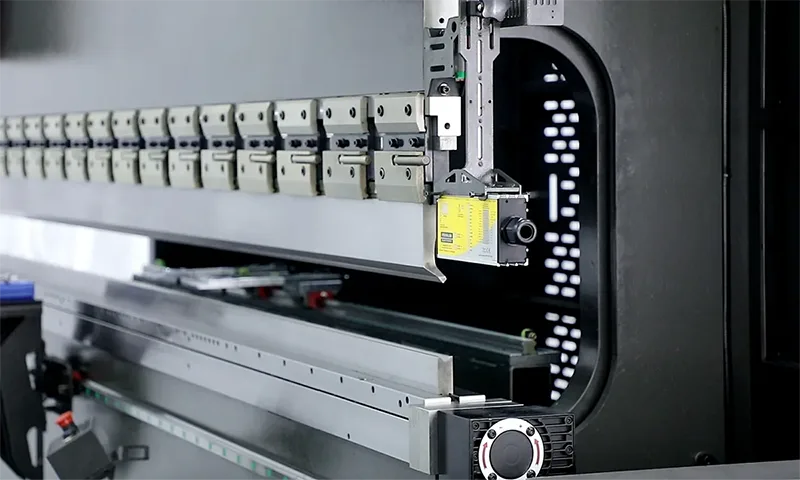
Enter your email address below and subscribe to our newsletter
A press brake stands as a cornerstone machine tool within the realm of metalworking. Its primary function involves the precise bending of sheet metal and other malleable materials into desired forms. This is achieved through a process where the workpiece is securely clamped between a specifically shaped punch and die. Subsequently, controlled force is applied, compelling the material to conform to the contours of the tooling, thus achieving the intended bend angle or overall shape. The significance of press brakes extends across numerous manufacturing sectors, highlighting their fundamental role in the creation of a vast array of metal components.
The journey of press brake technology reflects a continuous pursuit of enhanced precision and efficiency. Initially, these machines were operated entirely manually, demanding considerable skill and effort from the operator. Over time, innovations led to the introduction of Numerical Control (NC) systems, which automated certain aspects of the bending process based on pre-programmed instructions. This represented a significant leap forward in terms of repeatability and speed compared to manual methods. Further advancements culminated in the development of Computer Numerical Control (CNC) systems, which incorporate sophisticated computer technology to manage and execute complex bending operations with even greater accuracy and flexibility. This evolution underscores a clear trend towards increased automation and control in metal forming processes.
The term “NC” in the context of machinery refers to Numerical Control, a method of automating machine movements through the use of pre-programmed numerical data. This system allows for the machine to perform tasks automatically, guided by a sequence of numbers and symbols that dictate operational parameters. Unlike purely manual operations, NC introduces a level of automation that enhances consistency and reduces the need for constant operator intervention.
An NC press brake, therefore, is a type of press brake that utilizes a basic controller driven by pre-programmed numerical instructions to bend sheet metal and other materials into precise shapes. This automation allows for improved efficiency and repeatability in bending operations compared to traditional manual press brakes. The operator inputs specific numerical values that correspond to the desired bending angles, depths, and back gauge positions, which the machine then follows to execute the bending process.
It is important to distinguish NC press brakes from their more advanced counterparts, CNC (Computer Numerical Control) press brakes. While both types utilize automated control systems, CNC press brakes incorporate sophisticated computer systems that offer more advanced programming capabilities, real-time feedback, and greater flexibility in handling complex bending tasks. NC press brakes can be seen as occupying a middle ground in the spectrum of press brake technology, offering a significant upgrade from manual operation while remaining less complex and often more cost-effective than CNC machines.
The functionality of an NC press brake relies on several key features and components working in concert to achieve the desired bending results.
At the heart of an NC press brake is the Numerical Control System. This system uses numerical codes, entered by the operator, to automate the control of various machine functions. These functions typically include the movement of the back gauge, which positions the workpiece, and the stroke depth of the ram, which determines the bend angle. The NC system in these machines is generally simpler than the computer-driven control systems found in CNC press brakes. This relative simplicity can translate to lower initial cost and potentially easier maintenance.
The application of force required for bending is achieved through either Hydraulic or Mechanical Actuation. While older NC press brake models might employ mechanical systems, modern machines predominantly utilize hydraulic systems. Hydraulic systems offer precise control over the force applied, which is crucial for accurate bending of metal sheets of varying thicknesses and strengths. The hydraulic cylinders generate the necessary force to move the ram and bend the workpiece against the die.
NC press brakes offer Basic Programmable Functions that allow operators to input the parameters of the bending process, such as the desired angles or dimensions of the bends. The programming interface is typically less sophisticated than that of CNC systems. In some older NC machines, programming might even involve manual input directly into the controller or the use of punch tapes, which contain the sequence of instructions for the machine. While capable of automating bending sequences, the flexibility and complexity of programming are generally limited compared to CNC machines.
A critical component for achieving accurate bends is the Back Gauge Assembly. This mechanism ensures that the workpiece is positioned precisely before each bend. In NC press brakes, the back gauge is often motorized and its position is controlled numerically based on the programmed data. This automated adjustment of the back gauge significantly enhances the accuracy and repeatability of the bending process compared to manual positioning.
The Ram is the moving part of the press brake that holds the upper tool, known as the punch. During the bending operation, the ram moves downwards, applying force to press the metal sheet against the lower tool, the die, which is held in the bed of the machine. The vertical movement of the ram, including its speed and depth, is controlled by the NC system to achieve the programmed bend.
Many NC press brakes incorporate a Torsion Bar Synchronization system. This mechanical linkage, often a robust steel bar, forces the hydraulic cylinders on both sides of the ram to move up and down in unison. This ensures that the bending force is applied evenly across the width of the workpiece, resulting in more consistent bends. However, a key limitation of torsion bar synchronization is the lack of real-time feedback and the inability for the system to automatically adjust for variations in material or load distribution. This can lead to lower overall bending accuracy compared to the electro-hydraulic servo systems used in many CNC press brakes.
Despite the automation offered by the NC system, operators of NC press brakes may still need to perform Manual Adjustments to certain settings. These adjustments can include setting the clamping force that holds the workpiece in place and ensuring the initial alignment of the material with the tooling. The necessity for these manual interventions indicates that NC press brakes, while offering significant automation over manual machines, are not fully automated in the same way that some CNC press brakes are.
The operation of an NC press brake involves a sequence of steps, starting with programming the machine and culminating in the actual bending of the workpiece.
The first step is Programming the NC Controller. The operator inputs the numerical data that defines the desired bending parameters into the NC controller. This is typically done through a control panel integrated into the machine or, in some cases, via an external computer that communicates with the controller. The data entered includes information such as the required bending angle for each bend, the sequence in which the bends should be performed, and the positions of the back gauge that will determine the location of each bend on the workpiece. In older NC systems, this programming might have involved creating or loading instructions from punch tapes.
Once the program is entered, the next stage is Machine Setup. Based on the programmed data, the operator needs to physically set up the machine for the specific bending task. This involves selecting and installing the appropriate punch and die tooling required for the desired bend shape and angle 2. The operator also manually adjusts the back gauge based on the initial programmed settings to ensure the workpiece will be positioned correctly for the first bend. This setup phase requires operator skill and knowledge of tooling and machine operation.
With the program entered and the machine set up, the Bending Operation can commence. The operator initiates the bending cycle, and the NC system takes control of the machine’s movements. The ram, guided by the programmed instructions, moves downwards, carrying the punch to press the workpiece into the die. As each bend is completed, the back gauge automatically moves to the next programmed position, preparing the workpiece for subsequent bends in the sequence. This automated positioning of the workpiece by the back gauge is a key advantage of NC press brakes over manual machines, as it ensures consistency and accuracy across multiple bends.
Throughout the automated bending process, Monitoring and Adjustments by the operator are still important. The operator observes the machine’s operation to ensure that the bends are being formed correctly and that there are no issues with the material or the tooling. While the NC system automates the programmed movements, the operator may still need to make minor manual adjustments to fine-tune the process or to compensate for variations in material properties or machine behavior. This ongoing monitoring and potential for manual intervention highlight the semi-automated nature of NC press brake operation.
NC press brakes offer several benefits that make them a valuable tool in metal fabrication, particularly when compared to manual press brakes.
One significant advantage is Improved Consistency and Accuracy. The automated control of the bending process by the NC system leads to a higher degree of consistency in bending speed and accuracy compared to manual operation, where the results can vary depending on the operator’s skill and fatigue. By following pre-programmed instructions, the NC press brake can produce parts with more uniform bend angles and dimensions, reducing the likelihood of errors and rework.
NC press brakes also offer Increased Bending Speed and Efficiency. The NC system can control various aspects of the bending cycle, such as the speed of the ram’s descent and ascent, as well as the movement of the back gauge. This automation allows for faster processing times, especially for repetitive bending tasks, leading to increased production efficiency. The ability to program a sequence of bends allows the machine to perform multiple operations on a single workpiece with minimal operator intervention, further enhancing efficiency.
Another key benefit is the Reduced Reliance on Skilled Operators. While operating an NC press brake still requires training, it generally demands less specialized skill compared to performing complex bends on a manual machine. The automation provided by the NC system guides the bending process, making it easier for operators with less extensive experience to produce accurate parts. This can help businesses reduce labor costs and broaden their pool of potential operators.
NC press brakes typically represent a Cost-Effective Solution for many metal bending needs. They are generally less expensive to purchase than CNC press brakes, making them a more accessible option for smaller workshops or businesses with budget constraints. For operations that do not require the high level of complexity and flexibility offered by CNC machines, an NC press brake can provide a significant return on investment by improving efficiency and accuracy at a lower initial cost.
NC press brakes are particularly Suitable for Low to Medium Production Runs. They offer a good balance of automation and cost-effectiveness for production volumes that fall between manual operations and the high-volume capabilities of CNC machines. For tasks that involve a moderate number of parts or relatively straightforward bending operations, NC press brakes can provide a significant improvement in productivity and quality without the higher investment associated with CNC technology.
The Basic Programming Interface of NC systems can also be considered an advantage in some contexts. The use of numerical inputs for programming bending parameters can be easier for some operators to learn and understand compared to the more complex software-driven interfaces often found on CNC machines. This can lead to a quicker learning curve for new operators and easier programming for simpler bending tasks.
Despite their advantages, NC press brakes also have certain limitations and disadvantages, particularly when compared to CNC press brakes.
One significant limitation is Lower Accuracy Compared to CNC. The mechanical synchronization systems, often relying on a torsion bar, used in many NC press brakes lack the real-time error feedback and automatic adjustment capabilities found in CNC machines. This means that NC press brakes are generally less precise and may not be suitable for applications requiring very tight tolerances or complex bend geometries. The accuracy can also be affected by variations in material thickness or inconsistencies in the bending process that the machine cannot automatically compensate for.
NC press brakes offer Limited Flexibility and Automation. Compared to CNC machines, they provide less flexibility in handling a wide variety of bending tasks and offer a lower level of overall automation. Changes in production requirements often necessitate more manual reconfigurations of the machine, such as changing tooling and adjusting back gauge settings. This can make NC press brakes less efficient for high-mix, low-volume production environments where frequent changes between different parts are required.
The Limited Axis Control of NC press brakes also restricts their capabilities. Typically, NC machines control only two axes: the X-axis for the back gauge position and the Y-axis for the ram movement. In contrast, CNC press brakes can control additional axes, such as the R-axis for back gauge height, Z-axis for back gauge lateral movement, and even axes for independent movement of different parts of the back gauge. This greater control allows CNC machines to perform more complex bending operations, including tapered bends and bends with varying radii.
The need for Manual Adjustments Required by the operator can also be seen as a disadvantage. While NC systems automate the basic bending sequence, operators often need to manually fine-tune parameters like clamping force and material alignment. This reliance on manual intervention can introduce variability into the process and requires a certain level of operator skill to ensure consistent quality.
NC press brakes generally have Slower Operating Speeds compared to CNC machines. The descent and return speeds of the ram in NC press brakes are typically lower, which can impact the overall production time, especially for high-volume runs. CNC machines often utilize more advanced hydraulic systems and control mechanisms that allow for faster and more efficient bending cycles.
A structural limitation of some NC press brakes that utilize torsion bar synchronization is their inability to Handle Partial Loads Well. Prolonged operation with the bending force concentrated on one side of the machine can lead to deformation of the torsion bar, affecting the machine’s accuracy and longevity. CNC press brakes with independent control of the hydraulic cylinders on each side do not typically encounter this issue.
The Limited Program Storage capacity of NC press brakes can also be a drawback for operations that involve a variety of different parts. NC controllers typically have less memory for storing bending programs compared to CNC systems. This might require operators to manually re-enter program data for different jobs, which can be time-consuming and increase the risk of errors.
Finally, some NC press brakes have a Fixed Slide Opening Height. This means that the ram must travel from its highest point to its lowest point during each bending cycle, even if a smaller stroke would suffice. This can lead to inefficiencies in the bending process compared to CNC machines that offer more precise control over the ram’s position and stroke length.
The choice between an NC and a CNC press brake depends heavily on the specific needs and requirements of the metal fabrication operation. Several key differences distinguish these two types of machines.
The most fundamental difference lies in the Control System. NC press brakes utilize a simpler numerical control system where operators manually input specific data for each bend. This system typically allows for the control of only two axes (X and Y). In contrast, CNC press brakes employ a more advanced computer numerical control system that allows for complex programming, often integrated with CAD/CAM software, and can control multiple axes (typically at least 3+1 and often more). The CNC system can also provide real-time feedback and automatically adjust bending parameters to ensure higher accuracy.
In terms of Accuracy, CNC press brakes generally offer superior performance. Their advanced control systems, often coupled with feedback mechanisms like linear encoders, allow for precise control over bending angles and ram positioning. NC press brakes, relying on mechanical synchronization and manual adjustments, typically have lower bending accuracy and may require more manual intervention to achieve the desired results.
The Automation Level is another significant differentiator. CNC press brakes offer a higher degree of automation, often including features such as automatic tool changing, robotic material handling integration, and the ability to execute complex, multi-step bending programs with minimal operator intervention. NC press brakes require more manual involvement in setup, programming, and adjustments between bends.
Programming Complexity also differs considerably. CNC press brakes can handle intricate workpieces and complex bending sequences, often allowing for offline programming and simulation using specialized software. NC press brakes typically have a more basic programming interface that involves manually inputting numerical data for each bend, making them less suitable for highly complex or varied bending tasks.
Regarding Speed, CNC press brakes generally operate faster than NC press brakes. Their more advanced hydraulic systems and control algorithms allow for quicker descent and return speeds of the ram, as well as faster back gauge movements, leading to shorter cycle times and higher production rates.
The Cost of NC press brakes is typically lower than that of CNC press brakes, both in terms of initial purchase price and potentially in maintenance costs. However, the increased automation and efficiency of CNC machines can lead to lower labor costs and reduced material waste in the long run, potentially offsetting the higher initial investment for certain applications.
Finally, the number of Axes Control is a key distinction. NC press brakes typically control only the X (back gauge) and Y (ram movement) axes. CNC press brakes, on the other hand, can control a greater number of axes, including those for the back gauge (e.g., X, R, Z1, Z2) and sometimes even for tool manipulation, allowing for more complex and intricate bending operations.
The following table summarizes the key differences between NC and CNC press brakes:
Feature | NC Press Brake | CNC Press Brake |
Control System | Simpler numerical control, manual data input | Advanced computer numerical control, complex programming |
Accuracy | Lower, requires manual adjustments | Higher, with real-time feedback and automatic correction |
Automation Level | Basic automation, more manual intervention needed | High automation, often with robotic integration |
Programming | Simpler, numerical input, sequential operations | Complex, CAD/CAM integration, multi-step programs |
Speed | Slower descent and return speeds | Faster descent and return speeds |
Cost | Lower initial and potentially maintenance cost | Higher initial and potentially maintenance cost |
Axes Control | Typically 2 axes (X, Y) | At least 3+1 axes, often more |
Synchronization | Mechanical (e.g., torsion bar), no real-time feedback | Electro-hydraulic servo, real-time feedback |
Partial Load Handling | Poor, can deform torsion bar under prolonged use | Good, independent control of each side |
Program Storage | Limited | Extensive |
NC press brakes find widespread use across various industries for a range of metal forming applications. Their ability to bend sheet metal and other materials into specific shapes makes them essential tools in numerous manufacturing processes.
The Automotive Industry utilizes NC press brakes for manufacturing a variety of components, including body panels, brackets, and structural parts that require precise bending. Similarly, the Aerospace Industry employs these machines in the production of aircraft components, although the higher precision requirements of some aerospace applications may necessitate the use of CNC press brakes for more critical parts.
In the Construction Industry, NC press brakes are used to bend metal sheets into various shapes for building structures, roofing, and other architectural elements. The Electronics Industry relies on these machines for fabricating enclosures, chassis, and other metal parts used in electronic devices.
NC press brakes are also widely used in Light Industry and General Manufacturing sectors for a broad range of bending tasks, from creating simple brackets to more complex housings and enclosures. Industries such as Shipbuilding and Container Manufacturing utilize press brakes, including NC models, for bending the large metal plates required in their respective products. Furthermore, the manufacturing of Elevator and Railway Vehicles involves the use of NC press brakes to form various metal components.
NC press brakes are particularly well-suited for Small to Medium-Sized Production Operations where the complexity of parts and the required production volume do not necessitate the advanced capabilities of CNC machines. They offer a cost-effective way to improve efficiency and accuracy over manual bending methods for a wide array of metal fabrication tasks.
NC (Numerical Control) press brakes represent a significant advancement over manual press brakes, offering a level of automation that enhances consistency, speed, and efficiency in metal bending operations. By utilizing pre-programmed numerical data to control key machine functions such as ram movement and back gauge positioning, NC press brakes enable the production of more accurate and repeatable bent parts with reduced reliance on highly skilled operators. They serve as a valuable bridge between manual operations and the more sophisticated world of CNC (Computer Numerical Control) press brakes, providing a cost-effective solution for a wide range of low to medium production volume applications across various industries, including automotive, aerospace, construction, and electronics.
While NC press brakes offer numerous advantages, they also have limitations, particularly when compared to CNC machines. Their accuracy is generally lower due to the lack of real-time feedback and automatic adjustment capabilities, and they offer less flexibility and automation for complex bending tasks. The control systems are simpler, typically controlling only two axes, and operating speeds are generally slower.
When considering whether to use an NC press brake, factors such as the required production volume, the complexity of the parts to be bent, the budget constraints, and the necessary level of accuracy must be carefully evaluated. For businesses with simpler bending needs and limited budgets, an NC press brake can provide a substantial upgrade in efficiency and quality compared to manual methods. However, for operations requiring high precision, complex geometries, or high production volumes, a CNC press brake may be the more suitable investment. Ultimately, the choice between an NC and a CNC press brake hinges on a thorough understanding of the specific application requirements and a careful consideration of the trade-offs between cost, capability, and performance.