Breaking News
Popular News
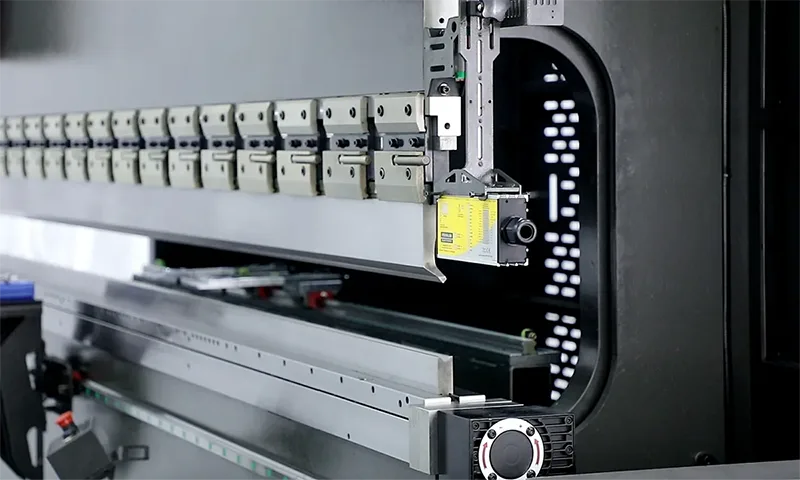
Enter your email address below and subscribe to our newsletter
The process of bending sheet metal and metal plates into specific shapes is a fundamental operation in numerous manufacturing sectors.
Press brakes, as specialized machines designed for this purpose, have long been essential tools in industries ranging from automotive and aerospace to construction and electronics. These machines apply controlled force to a workpiece, typically a sheet of metal, to create precise bends at predetermined angles.
Over time, advancements in manufacturing technology have led to significant enhancements in the capabilities and efficiency of press brakes. One of the most transformative of these advancements is the integration of Computer Numerical Control (CNC).
CNC represents a paradigm shift in manufacturing, introducing automation to the control, movement, and precision of machine tools through the utilization of pre-programmed computer software embedded within the machinery.
This report aims to provide a comprehensive understanding of CNC press brakes, detailing their definition, core components, operational principles, advantages over traditional press brakes, various types available, the programming and control systems that govern their operation, and their historical evolution, drawing upon the provided research material.
At its core, a press brake is a machine specifically designed for bending sheet metal and metal plates. Its primary function is to form predetermined bends in a workpiece by securely clamping it between an upper tool, known as the punch, and a lower tool, referred to as the die.
The process involves the application of substantial force, compelling the metal to permanently deform and conform to the shape defined by the tooling. The fundamental working principle of a traditional press brake involves positioning the material to be bent, the workpiece, between the punch and the die.
Subsequently, a powerful force is exerted by the ram, the moving component of the press brake that holds the punch, onto the workpiece. This applied force exceeds the material’s yield strength, causing it to deform and adopt the profile of the die, thereby achieving the desired bend angle or shape.
Several key components are integral to the operation of a traditional press brake. These include a robust frame and bed, which provide the necessary structural support to withstand the significant forces involved in the bending process.
The ram is crucial as it moves vertically, carrying the punch and delivering the bending force.
The punch and die, collectively known as the tooling, are responsible for imparting the desired shape to the metal. Lastly, a back gauge is often employed to accurately position the workpiece before the bending operation, ensuring the bend is formed at the correct location.
Computer Numerical Control (CNC) represents a pivotal advancement in the realm of manufacturing and machinery. The acronym CNC stands for Computer Numerical Control, highlighting the central role of computers in automating manufacturing processes.
In the context of manufacturing, CNC is a method that brings automation to the control, movement, and overall precision of machine tools. This automation is achieved through the use of pre-programmed computer software that is integrated directly into the machine tools themselves. CNC technology is widely applied in manufacturing to precisely machine parts made from various materials, including metals and plastics.
CNC systems are capable of controlling and operating a diverse range of machinery, such as lathes, milling machines, drills, and, significantly, press brakes, all through the power of computer commands. These machines operate by executing pre-programmed software and specific codes, such as G-code and M-code, which provide the machine with detailed instructions regarding the exact movements and tasks it needs to perform.
For instance, a CNC machine can precisely cut a piece of material, whether metal or plastic, based on the specifications pre-coded into the program, all without the need for direct manual control by a machine operator. This automation inherently leads to improved accuracy and a higher degree of consistency in production outcomes.
Instructions are delivered to a CNC machine in the form of a sequential program, comprising a series of machine control instructions.
Notably, CNC machining can accomplish complex, three-dimensional cutting tasks based on a single set of programmed prompts.
Compared to traditional, non-computerized machining methods that require manual operation or mechanical control via templates, CNC offers a substantial increase in productivity, particularly for repetitive production tasks.
Often, the design of a mechanical part is created using Computer-Aided Design (CAD) software, and then this design is translated into manufacturing directives by Computer-Aided Manufacturing (CAM) software, which are then loaded into the CNC machine.
A CNC press brake can be defined as a press brake whose bending process is automated and precisely controlled by an integrated Computer Numerical Control (CNC) system.
This advanced machine utilizes pre-programmed instructions to govern the movement of the ram, which applies the bending force, and the positioning of the workpiece, typically managed by a back gauge, thereby ensuring highly accurate and repeatable bends.
The CNC system takes on the crucial role of managing various bending parameters, including the angle of the bend, the depth to which the punch penetrates the die, and the sequence of multiple bends if required.
By integrating CNC technology, the fundamental capabilities of a traditional press brake are significantly enhanced, leading to improvements in precision, operational speed, and overall versatility in metal fabrication processes.
The automation afforded by CNC allows for the production of complex parts with intricate bend sequences and tight tolerances, which would be challenging or even impossible to achieve with manually operated press brakes.
The essential components of a CNC press brake largely mirror those of a traditional press brake, but with the significant addition of computer-controlled systems that enhance their functionality and automate their operation.
The frame and bed remain critical for providing the structural integrity and support necessary to withstand the immense forces generated during the bending process.
While CNC integration doesn’t fundamentally alter these structural elements, it necessitates that they are built to very high standards to ensure the stability required for automated, precise bending operations.
The ram, which houses the punch and applies the bending force, undergoes a significant transformation in a CNC press brake. Its vertical movement, typically designated as the Y-axis, is under the precise control of the CNC system.
This control is often achieved through sophisticated hydraulic or electric servo systems, allowing for programmable adjustment of the ram’s speed, position, and the amount of force it exerts.
This level of control far surpasses that of manually operated rams, leading to much greater accuracy and repeatability in the bending process.
The punch and die, or tooling, are the direct interface with the workpiece, shaping the metal into the desired form. CNC technology facilitates the use of a broader range of specialized tooling and enables the execution of complex bending sequences that may require multiple tool changes.
In some advanced CNC press brakes, these tool changes can even be automated, further increasing efficiency.
The CNC system can store detailed information about various tools and automatically adjust bending parameters based on the specific tool selected for a particular operation.
The back gauge is crucial for accurately positioning the workpiece before each bend. In a CNC press brake, the back gauge is typically motorized, and its movement along the X-axis (and sometimes additional axes like R and Z for more complex positioning) is precisely controlled by the CNC system based on the programmed bending sequence.
Multi-axis back gauges significantly enhance the ability to create complex part geometries with multiple bends at varying locations without requiring manual repositioning of the workpiece between bends.
The power source for the ram’s movement in a CNC press brake is typically either a hydraulic or electric system.
CNC systems exert fine control over the valves and motors within these systems to achieve the precise bending force and speed required by the program.
For example, CNC allows for the implementation of closed-loop hydraulic circuits that utilize servo valves and grating rulers to provide very accurate control over the hydraulic pressure and ram position.
In electric CNC press brakes, servo motors drive the ram, offering high precision and improved energy efficiency.
The CNC controller serves as the central “brain” of the machine. It typically consists of a computer control panel, often with a touch screen interface, through which operators can input bending parameters, program the sequence of operations, and monitor the machine’s status.
The CNC controller interprets the programmed instructions and translates them into precise movements of the machine’s various components, ensuring accurate and repeatable bending operations.
It also has the capability to store multiple programs for producing different parts.
Motor controls are essential for regulating the operation of the electric motors used in the press brake, including servo drives and variable frequency drives (VFDs), all under the command of the CNC system to achieve the required precise movements.
A synchronization system is particularly important in hydraulic CNC press brakes with multiple cylinders, as it ensures that the force is distributed uniformly across the workpiece, leading to consistent bending results.
CNC systems often employ sophisticated electro-hydraulic synchronization mechanisms for this purpose.
These systems may utilize feedback from linear encoders to monitor and maintain the synchronization of the ram’s movement on both sides, ensuring even bending along the entire length of the workpiece.
To compensate for the natural deflection of the bending machine’s frame under load, which can affect bending accuracy, some CNC press brakes are equipped with a crowning system.
In advanced CNC machines, this crowning system can be automatically controlled by the CNC to adjust in real-time based on the bending force and material properties.
A foot pedal is often included as part of the control system, allowing the operator to initiate or control specific functions, such as clamping or releasing the workpiece, often in coordination with the automated CNC sequence.
The various electrical components, sensors, and actuators within the CNC press brake are interconnected by a network of wiring and cables, all managed and monitored by the central CNC system.
Finally, modern CNC press brakes are equipped with a range of safety features, such as light curtains and sensors, which are often integrated with the control system to automatically halt operation if a potential hazard is detected, ensuring operator safety.
The operation of a CNC press brake is a highly automated process driven by pre-programmed instructions.
The initial step involves programming, where the operator inputs all the necessary bending parameters into the CNC controller.
This includes specifying the desired bend angle, the depth of the bend, the sequence of multiple bends if the part requires them, the properties of the material being bent (such as thickness and type), and information about the tooling (punch and die) being used.
This programming can often be done through user-friendly graphical interfaces or touch screens on the machine itself.
Alternatively, for more complex parts, the programming might be done offline using specialized CAD/CAM software on a computer and then transferred to the CNC press brake via a USB drive or a network connection.
A significant advantage of CNC systems is their ability to store and recall numerous bending programs, which greatly simplifies and speeds up the process of switching between different jobs.
Once the program is loaded, the operator proceeds to workpiece placement, carefully positioning the sheet metal workpiece on the bed of the press brake and aligning it against the back gauge.
The CNC system automatically controls the position of the back gauge according to the requirements of the first bend specified in the program.
For parts with multiple bends, especially those requiring bends at different locations along the workpiece, CNC-controlled multi-axis back gauges can move in various directions to ensure precise positioning for each subsequent bend in the sequence, eliminating the need for manual adjustments.
Often, the workpiece is clamped securely in place to prevent any unwanted movement during the bending operation, ensuring the accuracy of the bend.
In some CNC systems, this clamping action might also be automated as part of the programmed sequence.
The core of the bending process is the bending step itself. Here, the CNC controller sends precise signals to the hydraulic or electric system that powers the press brake, instructing it to move the ram downwards.
This downward movement forces the punch, which is attached to the ram, to press the sheet metal into the die, which is located on the bed of the machine.
The CNC system exerts very accurate control over the speed of the ram’s descent, its final position (which determines the bend angle and depth), and the amount of force applied.
To ensure the programmed accuracy is achieved, CNC systems often incorporate feedback mechanisms, such as encoders, which continuously monitor the ram’s position and provide this information back to the controller, allowing for real-time adjustments to be made if necessary.
If the part program includes instructions for repeat bends, the CNC system will automatically reposition the back gauge according to the specifications for the next bend in the sequence, and the bending process is repeated until all programmed bends are completed.
Once the final bend in the sequence is complete, or if the part only requires a single bend, the CNC system initiates the ram retraction, moving the ram back to its starting position.
Finally, the operator can safely remove the workpiece from the press brake. Advanced CNC press brakes may also incorporate features for monitoring and adjustment during the bending cycle.
For example, some systems use optical sensors to measure the actual bending angle in real-time and automatically adjust process parameters to compensate for variations in material properties or thickness, ensuring the final bend meets the required specifications.
The adoption of CNC technology in press brakes brings forth a multitude of significant advantages compared to their traditional, manually operated counterparts.
One of the most prominent benefits is the increased precision and accuracy that CNC systems offer.
By precisely controlling the movement and force applied during the bending process, CNC press brakes can achieve exact bending angles and dimensions, significantly reducing the occurrence of errors and minimizing material waste. Some advanced machines can even create bends with an accuracy within millimeters.
This high level of precision is often maintained through closed-loop control systems that provide continuous feedback and allow for real-time adjustments. Another key advantage is the enhanced repeatability and consistency in the bending of multiple parts.
Once a bending program is optimized, a CNC press brake can replicate complex bends across hundreds or even thousands of parts with minimal variation. The stored programs ensure that each subsequent part is bent to the exact same specifications, leading to a high degree of consistency in the final product.
CNC press brakes also offer enhanced efficiency and speed in production. Automation allows these machines to operate at faster speeds than manual counterparts, significantly reducing production time and increasing the overall throughput of a fabrication shop.
The ability to program multiple bends in a single setup further contributes to this efficiency. In some cases, the integration of automatic tool changers can further minimize the time required for setup between different bending operations.
The automation inherent in CNC press brakes leads to reduced labor costs. While skilled operators are still needed for programming and setting up the machine, the automated bending process requires less direct manual intervention and supervision, allowing operators to focus on other tasks.
The high accuracy of CNC bending also contributes to reduced material waste. By ensuring that each bend is made to the required specifications from the outset, the need for rework or scrapping of incorrectly bent parts is minimized, leading to more efficient use of materials and cost savings.
CNC press brakes offer significant flexibility and versatility in handling a wide range of materials, thicknesses, and complex designs. They can accommodate intricate designs and custom bending sequences that would be extremely difficult or impossible to achieve with manual bending techniques.
Moreover, CNC programs can be easily modified and adapted for different jobs, providing a high degree of flexibility in production.
Modern CNC press brakes are also equipped with improved safety features designed to protect operators. Automation itself contributes to a safer working environment by minimizing the need for manual intervention in potentially hazardous tasks.
Features such as light curtains, sensors, and emergency stop functions are commonly integrated into these machines.
While the initial investment in a CNC press brake might be higher than that for a traditional machine, the long-term cost-effectiveness can be substantial.
The savings realized through increased efficiency, reduced waste, and lower labor costs often offset the initial expenditure over time.
Despite the advanced technology involved, CNC press brakes often feature user-friendly interfaces and programming systems, making their operation simpler compared to the level of skill required for achieving consistent results with manual machines.
Finally, CNC press brakes are valuable not only for mass production but also for prototyping. Their accuracy and programmability allow for the quick and precise creation of prototypes, facilitating the design and development process.
The landscape of CNC press brake technology encompasses various types of machines, each designed with specific power sources and features that make them suitable for different applications in metal fabrication.
Hydraulic CNC Press Brakes are the most prevalent type in modern manufacturing. These machines utilize hydraulic fluid to generate the force required for bending, offering a consistent and precise application of power. They are capable of handling heavier materials and are often chosen for tasks that demand significant tonnage, such as in the automotive and aerospace industries for heavy-duty applications, and in construction for bending thick beams and structural components. Hydraulic systems can provide long stroke operations and the substantial force needed to bend thicker metal sheets accurately.
Mechanical CNC Press Brakes represent an older technology, now less common, that employs a mechanical flywheel to drive the ram. While generally less expensive and potentially simpler to maintain than hydraulic models, they typically offer lower precision and flexibility. However, they are known for their faster cycle times and greater accuracy in the middle of the stroke, making them suitable for high-speed, high-volume production of less complex parts and for certain construction applications requiring high-strength components.
Electric CNC Press Brakes, also known as servo-electric press brakes, are gaining popularity due to their energy efficiency, high precision, and quieter operation. These machines use servo motors to drive a ball screw or belt drive, exerting tonnage on the ram with great accuracy. They require less maintenance as they do not have hydraulic components that are prone to leaks. While their force capacity might be lower compared to hydraulic systems, limiting their use with very thick materials, they are ideal for high-precision applications such as in the electronics industry, for bending ducts and fittings in the HVAC sector, in light metal fabrication, and in the renewable energy sector.
Hybrid CNC Press Brakes represent a fusion of hydraulic and electric technologies. They typically use a hydraulic system that is controlled by servo motors, aiming to leverage the benefits of both types: the power and versatility of hydraulics with the precision and energy efficiency of electric systems. Hybrid models often offer reduced hydraulic oil consumption and lower energy usage compared to traditional hydraulic machines, making them suitable for a range of applications, including the automotive industry for chassis parts and body panels, the renewable energy sector, and general fabrication tasks involving both light and heavy materials. For very large-scale applications requiring exceptional bending force,
High-Tonnage Press Brakes are engineered. These machines are capable of bending extremely thick or large sheets of metal and are essential in industries such as shipbuilding, power generation, and the manufacturing of large transportation vehicles like trains and buses. When dealing with exceptionally long workpieces, Tandem Press Brakes are employed. These systems consist of two or more press brakes that operate in synchronized fashion to bend materials that would be too long for a single machine. They are used in construction for producing long beams and pillars, in aerospace for large aircraft components, and in shipbuilding. Finally, Portable Press Brakes are smaller, more flexible machines designed for ease of transportation and setup, making them suitable for on-site fabrication work and smaller workshops.
Type | Power Source | Key Advantages | Typical Applications |
---|---|---|---|
Hydraulic | Hydraulic Fluid | High force, versatility, accurate | Heavy-duty, automotive, aerospace, construction |
Mechanical | Flywheel | Fast cycle times, accurate in mid-stroke, simpler maintenance (potentially) | High-speed, high-volume production of less complex parts, some construction |
Electric (Servo-Electric) | Servo Motors | Energy-efficient, high precision, quiet operation, low maintenance | Electronics, HVAC, light metal fabrication, high-precision work |
Hybrid | Hydraulic & Electric | Balance of power and efficiency, energy savings, reduced noise | Automotive, renewable energy, general fabrication of mixed materials |
High-Tonnage | Hydraulic | Capable of bending very thick or large sheets | Shipbuilding, power generation, transportation |
Tandem | Hydraulic/Electric | Bending of extra-long materials | Construction of large structures, aerospace, shipbuilding |
Portable | Various | Compact, easy to transport and set up | On-site fabrication, smaller workshops |
The operation of CNC press brakes is governed by sophisticated programming and control systems that enable the automation and precision for which these machines are known.
Programming involves the operator defining the parameters of the desired bends. This typically includes specifying the angle of each bend, the depth to which the punch should travel, and the sequence in which multiple bends should be performed. This information is often entered through user-friendly graphical interfaces or touch screens located on the machine’s control panel.
For more intricate parts, programming can be done offline using specialized software installed on a personal computer. This offline software often allows for the creation and import of CAD/CAM files, providing a seamless transition from the design phase to manufacturing.
Many CNC systems offer 2D or even 3D visualization of the bending process, including simulations that can help identify potential collisions or errors before the actual bending takes place. The CNC system itself performs calculations to determine the necessary force and ram movement required for each bend. Once a program is created and optimized, it can be stored within the CNC controller’s memory and easily recalled for future use, which is particularly beneficial for batch production and repeat jobs.
The control systems are the heart of the CNC press brake, responsible for interpreting the programmed instructions and precisely controlling the machine’s movements and actions. Several leading manufacturers specialize in producing CNC control systems for press brakes, including Delem, Cybelec, and ESA.
These control systems offer a wide range of features, such as automatic calculation of the bend sequence, integrated angle measurement tools, collision detection capabilities, and the ability to control multiple axes of movement, including the Y-axis (ram), X-axis (back gauge forward and backward), R-axis (back gauge up and down), and Z-axis (back gauge left and right). Modern CNC controllers often feature intuitive touchscreen interfaces and support various programming modes, including both graphical and numerical input options.
The control system is responsible for managing the speed, direction, and torque of the motors that drive the ram, back gauge, and other motorized components of the press brake. To ensure accurate bending, feedback systems, which include sensors and encoders, continuously monitor the position, angle, and pressure during the bending process, providing real-time data to the CNC controller. In some advanced CNC press brakes, artificial intelligence (AI) is being integrated to further optimize bending parameters and even predict potential maintenance needs.
Connectivity features, such as Ethernet and wireless capabilities, are also becoming increasingly common, enabling easier data transfer, remote monitoring, and integration with other manufacturing systems.
The development of CNC press brake technology is a story of continuous innovation, evolving from simple manual machines to sophisticated computer-controlled systems.
The earliest forms of press brakes in the 1920s were basic mechanical devices that relied on manual force to bend metal.
A significant milestone was the granting of the first official patent specifically for a “press brake” in 1927.
The 1960s and 1970s saw the rise of hydraulic press brakes, which offered enhanced precision and greater force compared to their mechanical predecessors.
The first patent for a hydraulic press brake was issued in 1968, marking a major technological advancement.
A pivotal turning point in the evolution of press brakes was the introduction of Computer Numerical Control (CNC) technology, which began to be integrated in the 1970s and 1980s.
This transformation converted press brakes from manually operated machines into programmable systems capable of executing complex bending tasks with remarkable precision.
The first patent for a computerized numerical control press brake was granted in 1977.
While early CNC systems had more limited capabilities compared to the advanced controllers of today, they laid the foundation for the future of automated metal bending.
As technology continued to advance, servo motor-driven press brakes gained prominence, offering even more efficient and precise control over the bending process.
The integration of robotics with press brakes further enhanced automation by enabling automated material handling and manipulation, leading to increased operational speed and accuracy.
Recent developments in CNC press brake technology have focused on refining control systems, including the development of more intuitive graphical user interfaces and more sophisticated programming capabilities.
Significant advancements have also been made in safety devices for press brakes, with the first patent for an operator safety device based on a photoelectric sensor appearing in 1981.
Modern CNC press brakes now often incorporate smart systems that utilize sensors and artificial intelligence algorithms for real-time monitoring, adjustments, and optimization of the bending process.
The overall historical trend has been a progression from purely manual operation to the incorporation of mechanical power, followed by hydraulic power, and ultimately culminating in the sophisticated computer control and automation that defines CNC press brake technology today.
In summary, a CNC press brake is an advanced metal fabrication machine that utilizes computer numerical control to automate and precisely manage the bending of sheet metal and metal plates.
It builds upon the fundamental principles of a traditional press brake by integrating sophisticated computer systems that control the movement of key components such as the ram and back gauge, ensuring highly accurate and repeatable bending operations.
The core components of a CNC press brake include the frame, bed, ram, punch and die tooling, back gauge, and either a hydraulic or electric power system, all orchestrated by a CNC controller.
The working principle involves programming the desired bend parameters, precisely positioning the workpiece, and then using the automated control of the ram to apply the necessary force to form the metal into the specified shape.
The advantages of CNC press brakes over traditional models are numerous, including increased precision, enhanced repeatability, greater efficiency, reduced labor and material costs, and increased flexibility in handling complex designs.
Various types of CNC press brakes exist, including hydraulic, mechanical, electric, and hybrid models, each suited to different applications and production needs.
The programming and control systems of these machines have become increasingly sophisticated, featuring user-friendly interfaces, advanced simulation capabilities, and compatibility with CAD/CAM software.
The historical development of CNC press brake technology reflects a continuous drive towards greater automation, precision, and efficiency in metal fabrication.
Looking towards the future, it is anticipated that CNC press brakes will continue to evolve with further integration of artificial intelligence, the Internet of Things (IoT), and the use of advanced materials, leading to even more efficient, intelligent, and versatile metal forming solutions.