Breaking News
Popular News
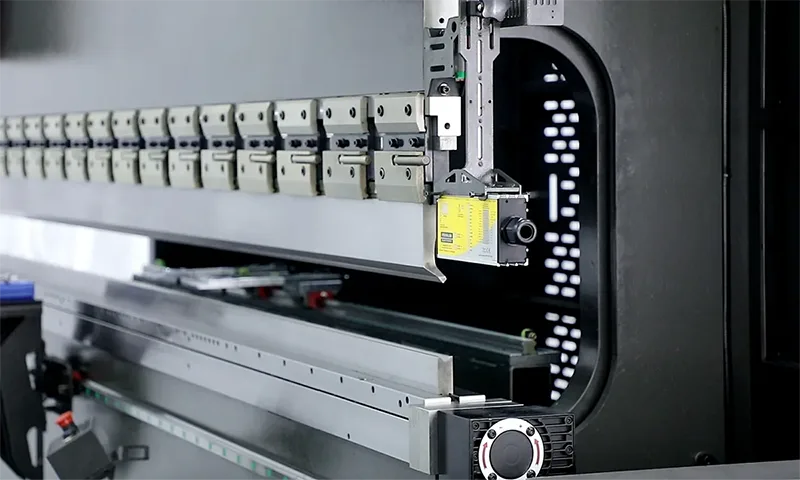
Enter your email address below and subscribe to our newsletter
Sheet metal forming on a press brake comes with a lot of myths—especially about press brake tooling. These myths can confuse you and slow down your work. By clearing them up, you can boost your productivity—making parts faster, cheaper, and better. Let’s dive into six common press brake tooling myths and see how busting them helps you work smarter.
Truth: You don’t always need separate tools. You can modify a standard die by grinding—carefully removing material—to make space for the metal to bend. This trick lets you create sharp bends, 90-degree angles, and offset (stepped) bends in one go. Check out Figure 1 to see how it works.
Limits: You can’t grind too much, or you’ll weaken the die. Also, tiny bends might not fit because the metal needs room to move. For medium or larger bends, though, this saves you from buying extra tools.
Productivity Boost: Fewer tools mean less setup time and lower costs. You finish jobs quicker with one die instead of switching between two.
Truth: Old machines stopped you from mixing angles to avoid crashes. Modern press brakes don’t care—as long as the punch doesn’t hit the die, you’re good. Look at Figure 2 for an example.
How It Works: If your punch bends at 86 degrees, you can’t make sharper bends than that without a collision. But you can pair one die with different punches. For instance, a 30-degree die works with 86-, 80-, or 75-degree punches for various jobs.
Productivity Boost: You save money by using fewer dies. Switching tools less often speeds up your workflow, especially on busy days.
Truth: Short tools cost less upfront, but they limit you. If you need to bend taller parts—like boxes or deep channels—you’ll end up buying taller tools later. Figure 3 shows why taller tools matter.
Smart Move: Think about your projects. Taller punches and dies handle deeper bends. Make sure your machine has space—at least 4 inches—for handling parts easily. Big machines with lots of room might need taller tools to reach the bending spot.
Productivity Boost: Buying the right height now avoids double spending. You’ll tackle more jobs without stopping to reorder tools.
Truth: Air bending is fast and flexible, but coining still shines for super-sharp bends—especially when the bend is tighter than the metal’s thickness. Figure 4 explains this.
Real Example: A company wanted to remake old products with tiny, precise bends. Air bending couldn’t cut it, so they used coining tools instead.
Tip: When picking a press brake, think about coining if you or your customers need exact, sharp bends.
Productivity Boost: Having coining as an option lets you take on special jobs others can’t, keeping customers happy and your shop busy.
Truth: You can air bend sharp corners, especially with thin metals. Figure 5 shows how.
Details: For thin steel (like 16-gauge), pick a die that’s six times the metal’s thickness. You’ll get bends that look sharp—close to the metal’s thickness. Thicker metals are trickier; they might crack if you push too hard. Bend across the grain to avoid trouble.
Productivity Boost: Sharp bends without extra tools save time and effort. You meet tight specs without slowing down.
Truth: One punch for all jobs sounds nice, but it wears out fast—especially with tough metals like stainless steel. Figure 6 has the details.
Guidelines: Match the punch tip to the metal:
Care Tips: Buy strong punches, keep them clean, and don’t overload them. They’ll last 10+ years.
Productivity Boost: Using the right tip prevents breakage and bad parts. You keep running smoothly without replacing tools constantly.
Understanding these truths helps you:
Next time you’re at the press brake, use these tips to work faster and smarter. You’ll see the difference in your productivity—and your bottom line!