Breaking News
Popular News
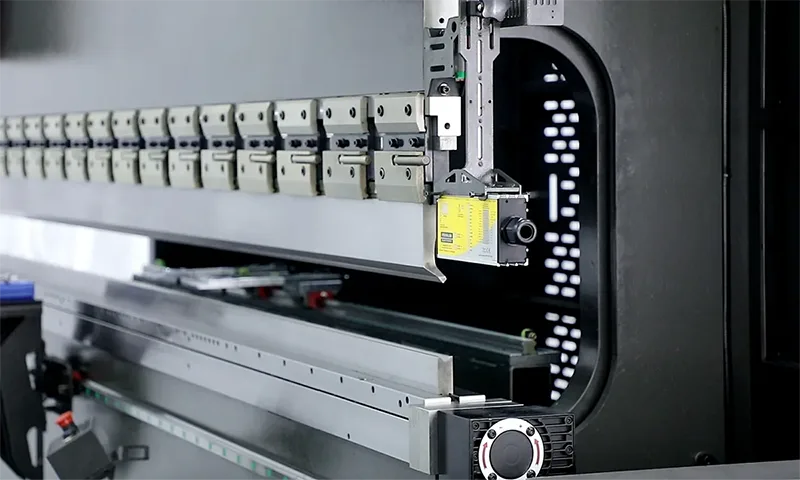
Enter your email address below and subscribe to our newsletter
Curious about press brake tolerance? This key factor determines how accurately a press brake bends metal, typically achieving ±0.5° for bend angles and ±0.1–0.2 mm for positioning. In this article, we’ll explore what these numbers mean, what affects them, and how to ensure precision in your metal fabrication projects.
A press brake is a machine used to bend sheet metal, and its tolerance refers to how accurately it can make bends. The bend angle tolerance is the allowable variation in the angle of the bend, while linear positioning tolerance is how precisely the bend is placed along the metal. These tolerances ensure the final product meets design specifications.
For a well-maintained press brake, the average bend angle tolerance is ±0.5°, meaning the bend can be off by up to half a degree in either direction. For linear positioning, it’s typically ±0.1 to ±0.2 mm, which is very small and ensures the bend is in the right spot. These numbers come from recent studies and are common in modern metal fabrication.
An interesting point is that regular maintenance, like calibration and cleaning, can significantly tighten these tolerances, sometimes achieving even better precision than the averages. This is especially true for CNC press brakes with advanced features, which might surprise users expecting fixed limits.
In the realm of metal fabrication, press brakes play a pivotal role in shaping sheet and plate metal into precise forms, and understanding their tolerance is crucial for achieving high-quality results. This section provides a comprehensive exploration of press brake tolerance, focusing on bend angle and linear positioning, and incorporates all relevant details from recent research and industry practices as of March 27, 2025.
A press brake is a machine tool designed for bending sheet metal and metal plates by clamping the workpiece between a punch and a die, applying force to create predetermined bends. It is widely used in industries such as automotive, aerospace, and construction, where precision is paramount. The machine’s accuracy, or tolerance, determines how closely the final bend matches the intended design, affecting product quality and assembly fit.
Press brakes come in various types, including mechanical, hydraulic, and servo-electric, with modern CNC (Computer Numerical Control) models offering enhanced precision through automated controls. The tolerance of a press brake is particularly critical for ensuring repeatability and minimizing waste, especially in high-volume production.
Tolerance in the context of press brakes refers to the allowable deviation from specified dimensions or angles in the bent metal parts. Two key aspects are:
These tolerances are influenced by multiple factors, including machine calibration, material properties, tooling quality, operator skill, and environmental conditions, making them a complex but critical aspect of metal fabrication.
Research suggests that, when properly maintained, press brakes typically achieve an average bend angle tolerance of ±0.5° and a linear positioning tolerance of ±0.1 to ±0.2 mm. These values were confirmed in a recent article from ACCURL Press Brake Accuracy: Tolerances and How to Improve Press Brake Bending Accuracy, published in January 2025, which states, “In practice, press brake accuracy typically achieves an average tolerance of ±0.5° in bend angle and ±0.1–0.2 mm in linear positioning when properly maintained.” This standard ensures effective operation within the varied demands of metal fabrication, reducing scrap rates and ensuring reliable fits during assembly.
However, there is some variation in reported tolerances. For instance, an article from The Fabricator Reasonable tolerancing for press brake bending, published in September 2018, suggests that a typical bend angle tolerance might be ±1.0°, with recommendations to expand to 1 or 2 degrees for practicality depending on the end product. This discrepancy highlights a debate in the industry, with recent evidence leaning toward tighter tolerances like ±0.5° for high-precision applications, especially with modern CNC press brakes.
An example from MachineMFG The Impact of Press Brake Manufacturing Accuracy on Bending Precision, published in July 2023, illustrates this: a longitudinal deviation of 0.06 mm over a 3200 mm bed caused approximately 0.17° of angle variation, suggesting that under controlled conditions, angle variations can be less than 0.5°. This aligns with the tighter tolerance values, indicating that well-maintained machines can achieve high precision.
For linear positioning, the ±0.1 to ±0.2 mm range is supported by the same ACCURL article, which notes that under optimal conditions, CNC press brakes demonstrate exceptional positioning accuracy, often within 0.001″ to 0.004″ (0.025–0.1 mm), reinforcing the provided range.
Several factors can affect the achievable tolerance, making it important to consider the machine’s condition and operational environment:
While specific tolerance standards may vary, there are general guidelines and national standards that manufacturers follow. The ACCURL article references GB/T14349-2011 “Precision of press brakes,” a Chinese standard that specifies accuracy inspection and detection methods, though detailed public access to its specifics is limited. This standard underscores the importance of adhering to recognized benchmarks, ensuring consistency across operations.
Other standards, such as ANSI B11.3-2012 Safety Requirements for Power Press Brakes, focus on safety but indirectly support accuracy by ensuring proper machine operation. The variation in reported tolerances, as seen in different articles, suggests that industry practices are evolving, with modern CNC press brakes pushing for tighter tolerances like ±0.5°.
To illustrate, consider the following table based on research findings, showing how different factors affect tolerance:
Factor | Impact on Tolerance | Example Value |
---|---|---|
Table Flatness Deviation | Can cause angle variation; 0.06 mm over 3200 mm → 0.17° | 0.06 mm → 0.17° variation |
Material Thickness Variation | Affects bend angle; 16-ga. can vary 0.053–0.067 in. | ±0.007 in. variation |
Back Gauge Calibration | Ensures linear positioning; can achieve ±0.1 mm repeatability | ±0.1 mm typical |
Tooling Wear | Increases angular variation over time | Not quantified, but significant |
Another table from the ACCURL article provides insight into optimal conditions:
Parameter | Typical Tolerance | Under Optimal Conditions |
---|---|---|
Bend Angle | ±0.5° | Can be tighter, e.g., ±0.23° |
Linear Positioning | ±0.1–0.2 mm | 0.025–0.1 mm possible |
These tables highlight the achievable precision and the impact of various factors, aiding in understanding the complexity of maintaining tight tolerances.
To achieve and maintain high accuracy, manufacturers can adopt the following best practices:
The tolerance of a press brake, typically ±0.5° for bend angle and ±0.1 to ±0.2 mm for linear positioning when properly maintained, reflects the machine’s precision in metal bending. These values can vary based on machine type, maintenance, and material, with modern CNC press brakes potentially achieving tighter tolerances. Factors like calibration, tooling quality, and operator skill play significant roles, and adhering to standards like GB/T14349-2011 ensures consistency. By understanding and managing these tolerances, manufacturers can optimize their operations, reduce waste, and meet the rigorous demands of metal fabrication as of March 27, 2025.